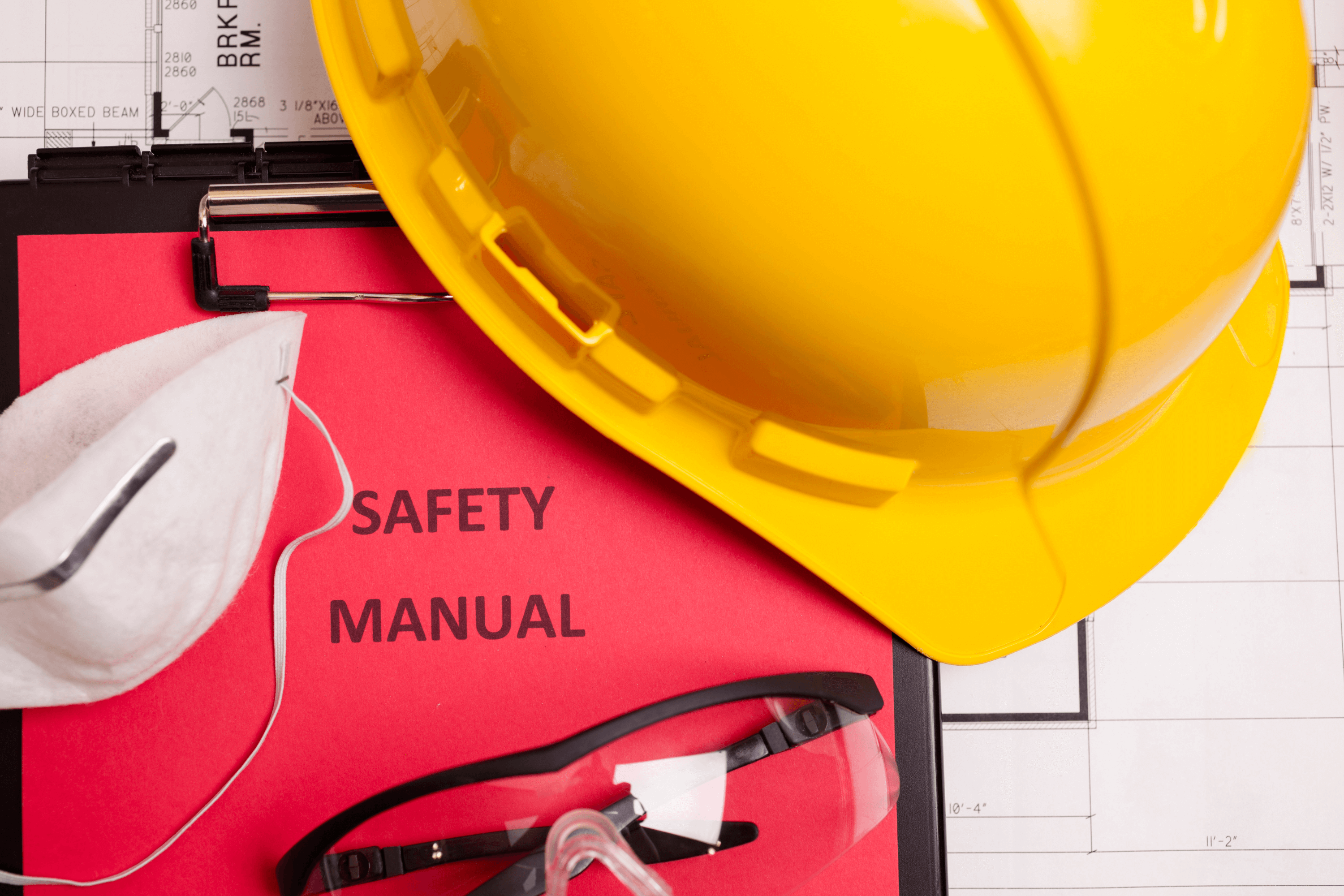
by Julia Kunlo, Evolution Safety Resources on September 12, 2017
When working with a new client, we start our relationship by asking for an overview of their Safety Management System (also called an SMS). The response we usually receive is, “Here is our safety manual.” While a safety manual is an important component of a Safety Management System, it alone does not have the power to protect your business and your employees. An SMS is a comprehensive and structured means of ensuring that your organization achieves and maintains high standards of safety performance – it is a collection of efforts, policies, and strategies that work together to keep your team safe. Beyond resulting in regulatory compliance and reduced incident rates, well-crafted Safety Management Systems improve quality, increase employee retention, enhance customer relations, and ultimately increase profits.
There are various types of Safety Management Systems to use as a guide for your company. Examples include Voluntary Protection Programs (VPP), Injury and Illness Prevention Plans (I2P2), ANSI Z10, and various ISOs. Though all types have merit, we refer to the National Safety Council’s “Nine Elements” as areference guideline. This type of SMS incorporates nine initiatives that, when working together, generate a top-level Safety Management System. These elements are grouped into three areas of focus – Administrative/Management, Operational/Technical, and Cultural/Behavioral.
Administrative/Management
The Administrative/Management pillar encompasses the policies, procedures, and priorities set by executives regarding their safety goals. To succeed in this area, it is important that all members of management understand, verbally support, and show passion regarding their safety program. There must be clear and structured guidelines that provide for the planning, execution, and measurement of safety efforts within the organization and systems in place for documenting progress. The three elements within the Administrative/Management pillar include:
- Management leadership and commitment
- Organizational communications and system documentation
- Assessments, audits, evaluations, and continuous improvement
Operational/Technical
Operational/Technical efforts encompass the systems in place to protect employees as they perform their workplace responsibilities. The first step in tackling this section of your Safety Management System is the creation of an in-depth Activity Hazard Analysis (AHA), which outlines the potential hazards associated with specific tasks as well as the means to overcome them. Once hazards are identified, your organization should engineer solutions and create operational guidelines to reduce the risk of injury while at work. Elements of the Operational/Technical pillar include:
- Hazard recognition, evaluation and control
- Facility design and engineering
- Operational safety programs
Cultural/Behavioral
The final and perhaps most influential pillar of a Safety Management System is Cultural/Behavioral. Related to the engagement of all levels of employees and a belief in shared responsibility, this pillar answers the question “Who is responsible for safety at my company?” with a responding “I am”. Teamwork, feedback, positive recognition, and employee engagement in safety efforts aid in supporting this worthy goal. The three elements of the Cultural/Behavioral pillar are:
- Employee involvement
- Motivation, behavior, and attitude
- Training and Orientation
As you can see, Safety Management Systems aren’t as simple as a collection of written policies, i.e., a safety manual; a true SMS requires an in-depth analysis of current efforts and goals for continuous improvement. When generating your own SMS, start off by establishing clear objectives, allocating resources, and conducting a gap analysis to find areas in need of immediate improvement. Above all, remember that your Safety Management System must meet the reality of your organization. The best programs are the ones that incorporate in-place policies and current procedures. If you are in need of assistance, there are experts in the field who specialize in developing systems that are top-level as well practical to your company.
Originally posted on GroundBreak Carolinas