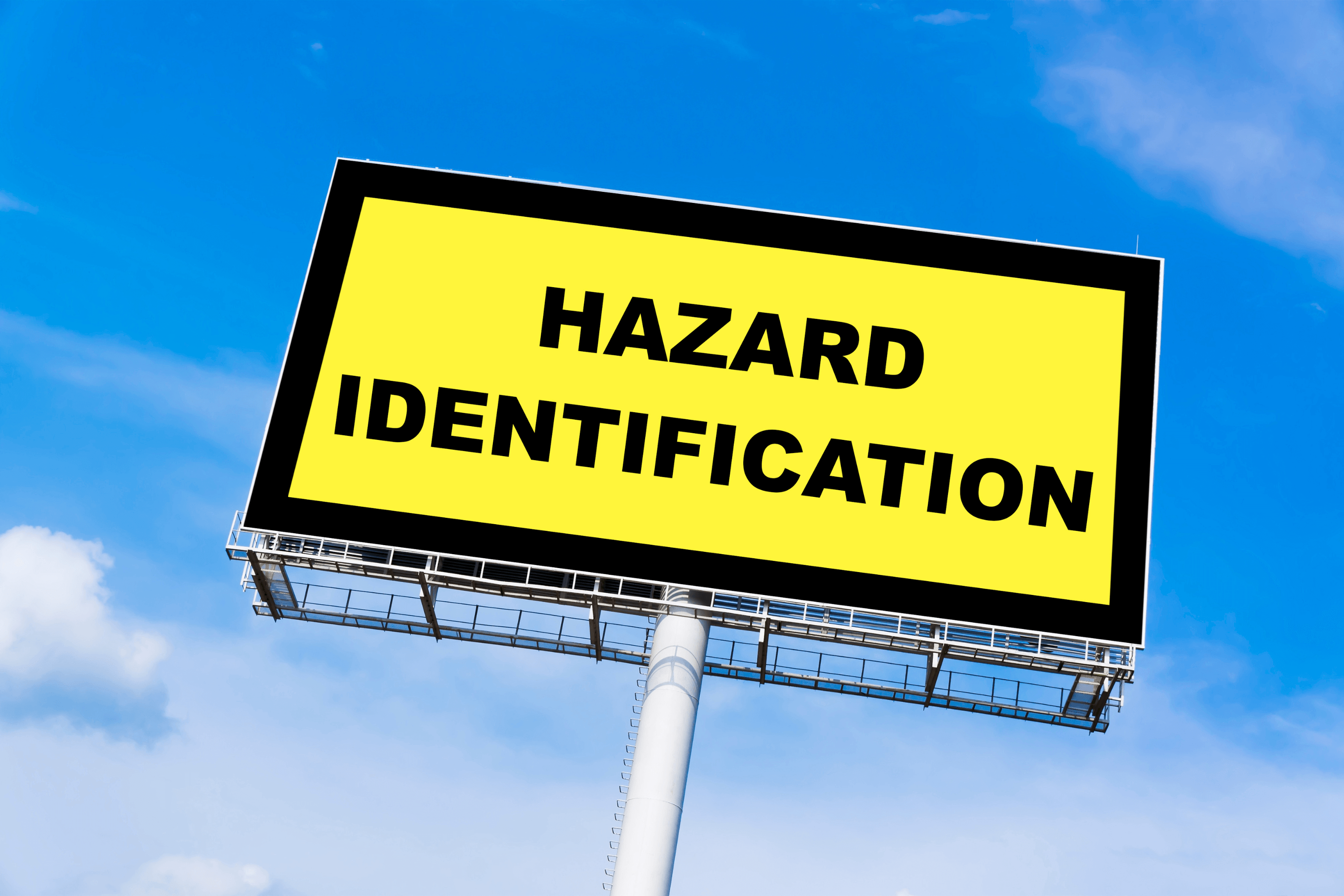
by Julia Kunlo, Evolution Safety Resources on November 27, 2018
We are pleased to continue with our GroundBreak series “Your Safety Manual Isn’t Enough.” While discussing the importance of building a safety program beyond a written manual, our series focuses on the need for a Safety Management System (SMS) while exploring common SMS components. Safety Management Systems are a collection of efforts, programs, and strategies that work together to keep your team safe – they look beyond written words and into corporate action. Most importantly, they look beyond compliance and into best practice. We previously noted the National Safety Council’s Nine Elements as a collection of common SMS principles. In this article, we will discuss the fourth element in this collection – Hazard Recognition, Evaluation, and Control. This element recognizes that all injuries are preventable; that management is responsible for finding and fixing hazards proactively.
The first step in creating and implementing any program is to write it down. Following suit, the first step in putting together a program for hazard recognition, evaluation, and control is to develop a written procedure. How will your company identify hazards? Do employees have the ability to report unsafe conditions in the field? How will you rate the severity of your findings? What means are available for controlling risk? Answering these questions is a great way to start your written program. Here is our challenge to you: As you read the rest of this article, jot down notes and inspiration to help you write a procedure for your company. Once clearly outlined on paper, you will find it much easier to train your employees on your company’s expectations.
Recognition
The employees who are faced with hazards are your best tools for understanding risk in your company – what challenges do they face? What tasks make them feel uneasy? What shortcuts do they take? By creating a systematic process through which employees can report these conditions and feelings, you are setting yourself up for successful hazard recognition program. Hazard recognition should be inclusive of chemical, physical, biological, ergonomic, and external (e.g., temperature) conditions. While the best source of information is an employee performing a regular task, it is also helpful to have employees observe their co-worker’s habits and report hazards they’ve gone “blind” to. The system should encourage the reporting of risk and should include methods/expectations for discussing follow up controls. Potential means for recognizing and reporting hazards include review of:
- AHAs/JHAs
- Near Miss Reports
- Perception Surveys
- Incident Investigations
- Jobsite Inspections
Evaluation
Once an effective recognition program is in place, you may become saturated with reports of tasks that employees deem hazardous. How do you begin to categorize this information? Are there patterns yet to be discovered? How can you understand what your first priorities should be? An organized means of evaluating hazards in the workplace ensures that all reports of risk are analyzed in the same way. Based on the results of the analysis, reactions can be made based on the risk category. A common means of evaluating hazards is to do so by assessing severity (from negligible to catastrophic) as well as probability (from minimal to high). You want to ask yourself “How likely is this event to occur?” as well as “What level of crisis would there be if the event occurred?”
Regardless of your tools for evaluation, it is important to ensure that you are evaluating the root cause of the risk and not just the visible hazards. To determine root cause, investigate and uncover conditions that allowed the hazard to exist – examples may be improper supervision, inadequate training, defective materials, etc. Eliminating the visible hazard is a band aid; treating the root cause heals the wound.
Control
Once the hazard has been recognized and evaluated, it is time to control the risk and protect your employees. Your company’s control program should consider budget, available technology, past efforts, etc. There are a multitude of solutions for every problem, and the solution that is best will be unique to your company. Regardless of the specific decisions you make, the Hierarchy of Controls should be used as a guide.
- Engineering Controls
- Engineering Controls are the most efficient at reducing risk; they eliminate the hazard, isolate people from the hazard, or substitute a part of the process to reduce the hazard.
- Administrative (policy, procedure)
- If engineering controls are not possible, Administrative Controls should be used. Administrative Controls include work practices and procedures that help to reduce/eliminate a hazard (ex: job rotation, safety rules, etc.).
- Personal Protective Equipment (PPE)
- As the last line of defense, consider PPE as a means of controlling hazards. PPE is the least effective control because if PPE fails, the hazard still exists.
How many of you accepted our challenge and began an outline of your Hazard Recognition, Evaluation, and Control program? If so, please send to Evolution Safety Resources for a no-cost consultation and review. You’ve taken a proactive step in keeping your employees safe, and we want to support you free of charge.
Originally posted on GroundBreak Carolinas