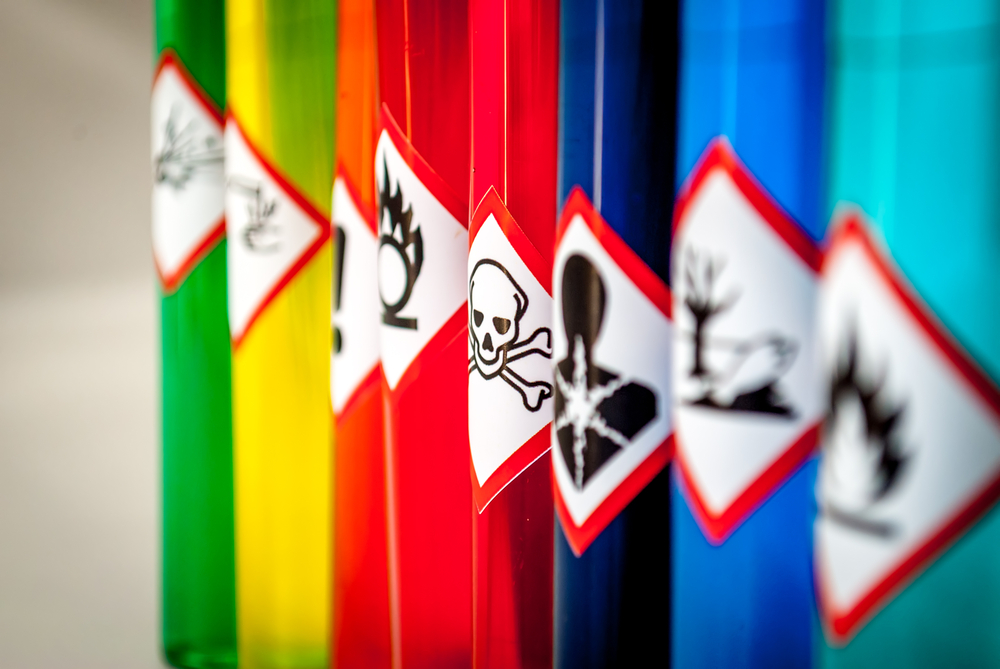
INTRODUCTION
Chemicals have become an important element of almost every aspect of modern life. All of these chemicals from cleaning fluids to pharmaceuticals, pesticides, and paints—are produced in workplaces, and may be used in workplaces downstream. While these chemicals have utility and benefits in their applications, they also have the potential to cause adverse effects. These negative effects include both health hazards (such as carcinogenicity and sensitization), and physical hazards (for example, flammability and reactivity properties). In order to protect workers from these effects and to reduce the occurrence of chemical source illnesses and injuries, employers need information about the hazards of the chemicals they use, as well as recommended protective measures. Workers have both a right and a need to know this information too, mainly so that they can take steps to protect themselves when necessary. No one knows exactly how many chemicals may be present in American workplaces. The total number of chemical substances that have been developed and registered in the Chemical Abstracts Service Registry reached 65 million in 2020—the last 10 million of those were added in less than two years. Many of them involve innovations such as the application of nanotechnology. While not all chemicals are produced commercially today, this vast number indicates the scope of the potential problems in workplaces with regard to the safe use of chemicals. In addition, most chemical substances are formulated into mixtures for use in the workplace. Therefore, the number of unique chemical mixtures is far greater than that of substances, and most workers are exposed to mixtures.
While most people can readily associate working in a chemical manufacturing plant with being a job that involves chemical exposures, there are many other types of facilities where such usage is also commonplace. For example, construction workers may be exposed to paints, lacquers, thinners, asphalt fumes, or crystalline silica. All of these types of exposures are of concern in terms of protecting workers and ensuring that chemicals are used safely.
OSHA’s Hazard Communication Standard OSHA’s HCS, 29 CFR 1910.1200, addresses the informational needs of employers and workers with regard to chemicals. The HCS was first promulgated in 1983 and covered the manufacturing sector. It was later expanded to cover all industries where workers are potentially exposed to hazardous chemicals.
Under the HCS, an employer must prepare and implement a hazard communication program for workers potentially exposed to hazardous chemicals. Your suppliers must provide hazard information in the form of labels on containers and SDSs when you receive a chemical. The focus of the information is to provide the identities and hazards of the chemicals, their characteristics and properties, and how potential adverse effects can be prevented. A “hazardous chemical” means any chemical which is classified as a physical hazard or a health hazard, a simple asphyxiant, combustible dust, pyrophoric gas, or hazard not otherwise classified. In addition to the health and physical hazards listed below, there may be some hazards that do not meet the specified criteria for the physical and health hazard classes. In these cases, the chemical manufacturer or importer will designate the hazards as “hazards not otherwise classified” (HNOC) and must provide information on the SDS to ensure that downstream employers are aware of these other effects and any appropriate protective measures.
Health Hazards
- Acute toxicity
- Skin corrosion/ irritation
- Serious eye damage/ eye irritation
- Respiratory or skin sensitization
- Germ cell mutagenicity
- Carcinogenicity
- Reproductive toxicity
- Specific target organ toxicity – single and repeated exposure
- Aspiration hazard
- Simple asphyxiant
Physical Hazards
- Explosives
- Flammable gases
- Flammable aerosols
- Oxidizing gases
- Gases under pressure
- Flammable liquids
- Flammable solids
- Self-reactive chemicals
- Pyrophoric liquids
- Pyrophoric solids
- Pyrophoric gas
- Self-heating chemicals
- Chemicals which in contact with water, emit flammable gases
- Oxidizing liquids
- Oxidizing solids
- Organic peroxides
- Corrosive to metals
- Combustible dust
WRITTEN HAZARD COMMUNICATION PROGRAMS
All workplaces where workers are exposed to hazardous chemicals must have a written hazard communication program that describes how the HazCom standard is implemented in that facility. When hazard communication is implemented effectively, it has significant benefits for both the employer and the workers in the workplace. Employers need the information provided to them in order to assess the safety and health aspects of their work appropriately and to select needed control measures for the chemicals that are present. The information provided on SDSs may also be used by employers to select the least hazardous chemical available to accomplish what is needed in the workplace. Substitution of a less hazardous chemical benefits workers because they will not be exposed to the greater hazards, and benefits employers because they may have less need for controls in some situations. The information employers receive on labels and SDSs will help them meet the requirements for a safe and healthful workplace.
CONCLUSION
OSHA believes that the Hazard Communication Standard is of critical importance to ensuring that hazardous chemicals are identified and that proper measures are implemented in workplaces to achieve safe use and handling. By understanding the hazards of the chemicals and using available information to pick the proper control measures to address these hazards, employers can achieve many benefits for themselves, as well as for their exposed workers. If you need help implementing an effective hazard communication program, contact us today. Our Evolution Safety Resources team is here to help you every step of the way.