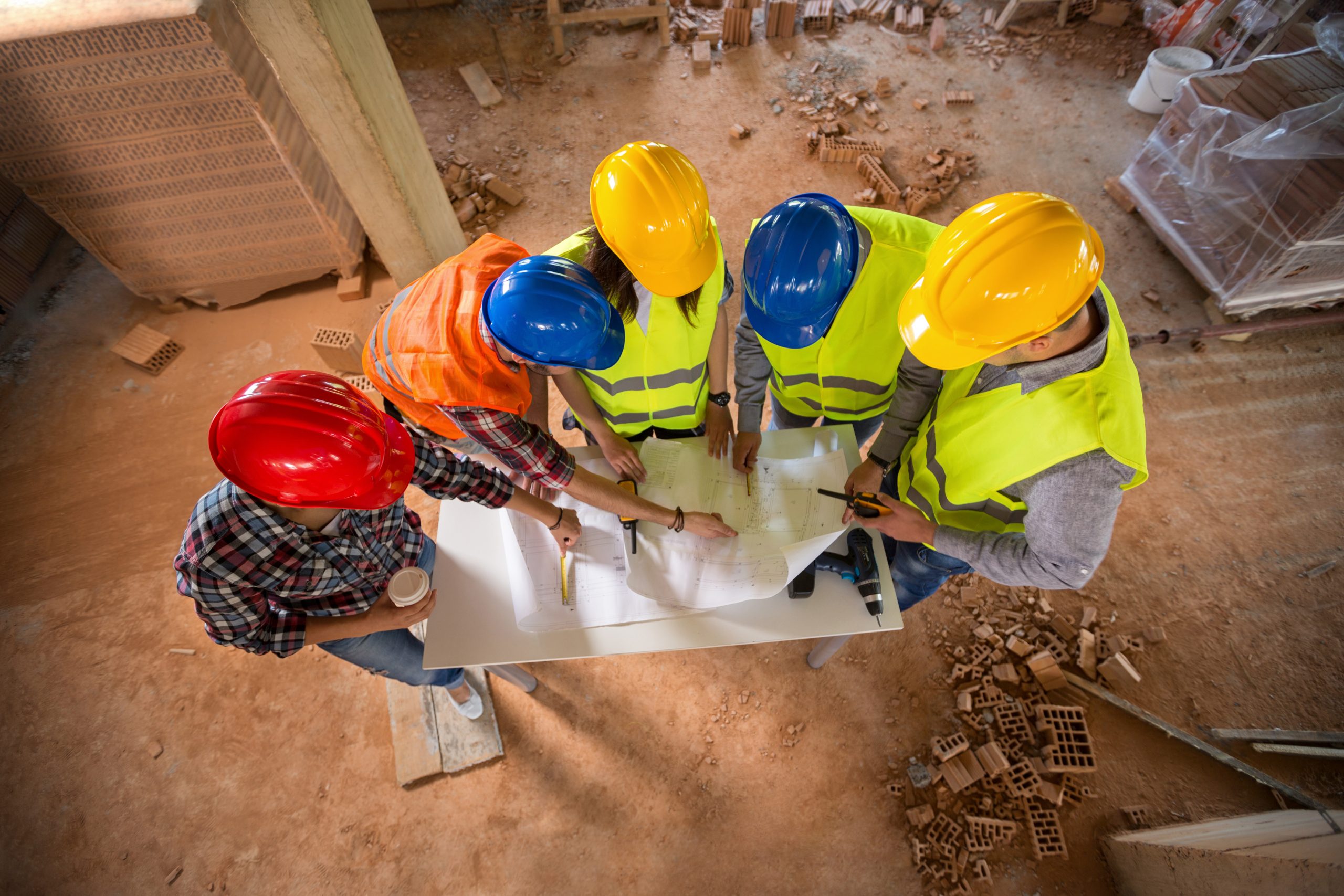
By Evolution Safety Resources | Posted on: April 13, 2022
The prevention of head injuries is an important factor in every safety program. Controlling the hazards that lead to head injuries is usually difficult to anticipate, so hard hats must be used to eliminate these risks. Data from the Bureau of Labor Statistics show: Hard hats were worn by only 16% of workers who sustained head injuries on the job. In just about any given year, more than one thousand workers are killed in the US from head injuries sustained at work. Workers complain that hard hats are hot and uncomfortable to wear. They state they “have never been hit by anything while doing their job, therefore wearing a hard hat is not needed.” The fact is Hard Hats Save Lives.
When Does OSHA Require Hard Hats?
OSHA has two standards that govern hard hat requirements:
29 CFR 1910.135 governs hard hat requirements for general industry workers
29 CFR 1926.100 refers to head protection requirements for construction, demolition, and renovation workers
Both standards require workers to wear hard hats when there is a potential for head injury from impacts, falling or flying objects, or electrical shock. Different kinds of tasks and situations call for different kinds of hard hats, so it’s important to know the difference between the ANSI-defined classes and available hard hats.
Hard Hat Types
All hard hats can be divided into two types – Type I and Type II.
- Type I: hard hats designed to protect workers from objects and blows that come from above and strike the top of a helmet.
- Type II: hard hats designed to offer protection from lateral blows and objects. This includes from the front, back, and side as well as from the top. Type II hard hats are also tested for off-center penetration resistance and chin strap retention.
Hard Hat Classes
Hard hats are also divided into classes that indicate how well they protect against electrical shock.
- Class E (Electrical): hard hats that can withstand up to 20,000 volts of electricity
- Extensively used by electrical workers
- Class G (General): hard hats that are able to withstand 2,200 volts of electricity
- Used in mining, building construction, shipbuilding, tunneling, timber and lumber operations, and manufacturing
- Class C (Conductive): hard hats that offer no voltage protection
- Also known as safety hats, caps, or bump helmets and used where there is the risk of bumping your head against fixed objects
- Specifically designed for lightweight comfort and impact protection.
- Normally used in certain construction and manufacturing occupations, oil fields, refineries, chemical plants where there is little danger of electrical hazards
When Should You Replace Your Hard Hat?
Hard hats must be replaced if they show signs of damage (dents, cracks, penetration, or fatigue due to rough treatment). It is essential to inspect hard hats for damage and signs of fatigue each time they are used. In addition to visual inspections, another way to test a hard hat is to grasp it in two hands and apply force by squeezing the hat. If you hear creaking or other unusual sounds, it is time to replace the hard hat.
While OSHA has no specific provision for an expiration date, manufacturers are allowed to determine if their equipment expires on a specific calendar date. In lieu of an expiration date, a generally accepted rule is to replace the support strap yearly and to replace the hard hat every five years. Harsh chemicals and extreme temperatures can make a hard hat degrade more quickly. Be sure to check with the manufacturer for guidelines on hard hat replacement and maintenance.
A hard hat may also expire if OSHA adopts more rigorous requirements. It is essential to regularly check OSHA standards for changes that may require your PPE to be updated.
Final Thoughts
Since hundreds of American workers suffer from fatal head injuries every year, hard hats are crucial features of worksite safety. At least one of these injuries is directly caused by a worker not wearing a hard hat.
Although the benefits of wearing a hard hat are obvious, the question remains –should a worker wear a hard hat if there is no apparent danger to the head from anything around? The answer is yes. Even when there is no obvious danger to the worker at that moment, the environment he or she works in can prove unexpectedly hazardous. In fact, those situations are what the hard hat is made for: defending workers from sudden dangers, when they don’t have the time or space to move out of the way. Wear your hard hat at all times that you are required to. Hard hats save lives.
If you need assistance understanding the OSHA standards or you’re interested in learning about the steps we take to ensure workplace safety and compliance, let’s get the conversation started today. Our experts at ESR are ready and available to help. We offer free consultations and will develop complimentary improvement plans.
Interesting Facts About Hard Hats
The “Hard-Boiled Hat”
- The hard hat was invented by Edward W. Bullard in 1919 to protect miners from head injuries.
- The original hard hat was made out of steamed layers of glued canvas painted black.
Hoover Dam
- The first project in which hard hats were widely used, was the construction of the Hoover Dam.
“Hard Hat Area”
- The first project in which hard hats were required on-site, was the construction of the Golden Gate Bridge in San Francisco.
Aluminum
- In the 1930s, aluminum was the standard material for hard hats.
Ventilated Hard Hats
- Ventilated hard hats, designed to keep the wearer’s head cool, were introduced in 1998.