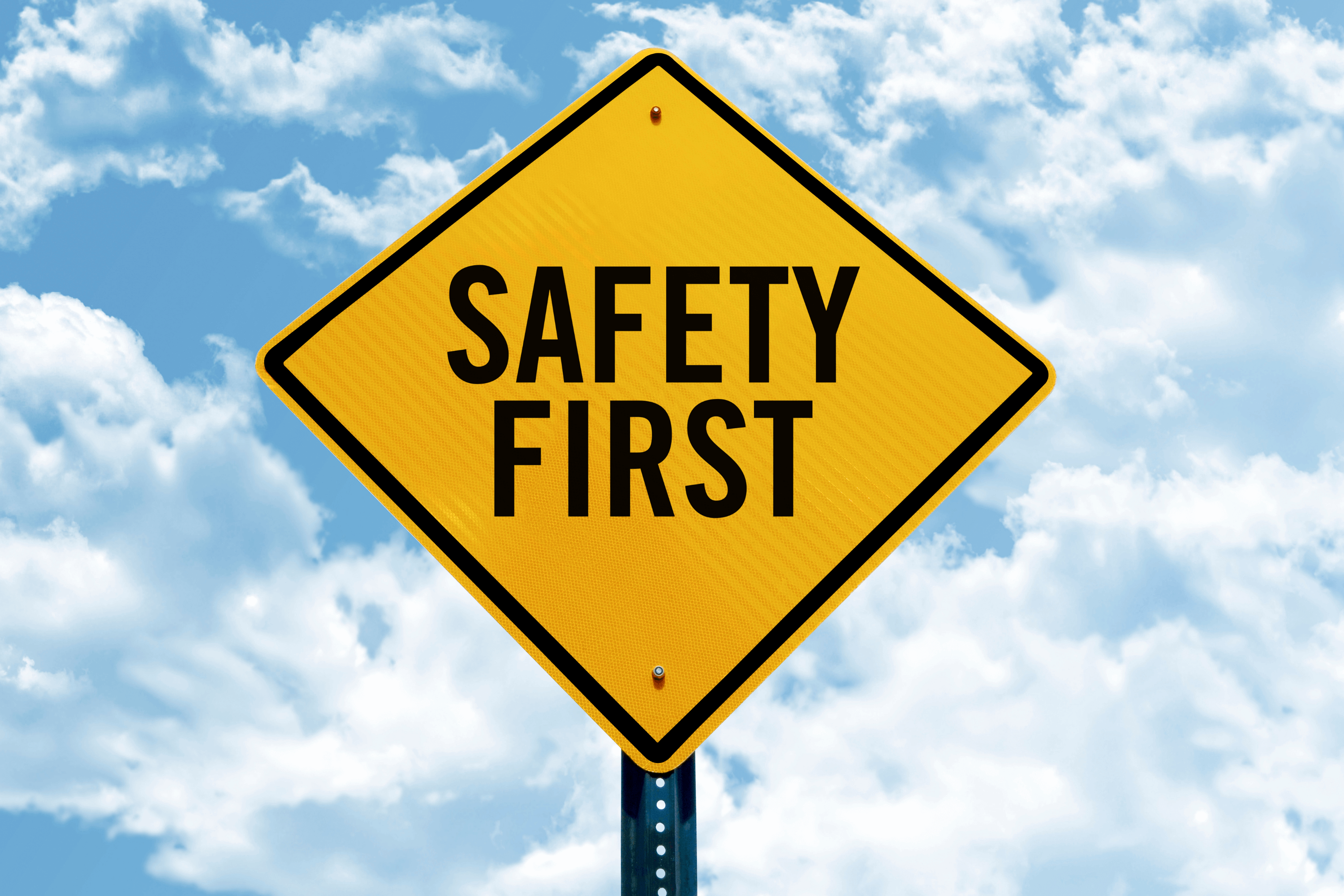
by Julia Kunlo, CSP, Evolution Safety Resources on November 22, 2019
Evaluating Safety’s Return on Investment (ROI)
When discussing corporate safety, it is common to hear catchy taglines such as: “Safety is #1; Safety is Our Top Priority; Safety Above All Else; and Safety First”. As an occupational safety consulting firm, we are thrilled to hear that organizations are placing a high value on safety when considering their daily operations. The fact of the matter, unfortunately, is that most of these taglines are just not true. Businesses do not focus on safety first because they must focus on profitability first. And while business owners should choose to only be profitable as long as they are safe, we understand that safety cannot realistically be seen as a line item without a budget. Considering the financial implications, how can companies protect their bottom line while also protecting their employees?
The information provided in this article should be used as a tool for deciding which components of a safety program to prioritize when all components cannot be reasonably afforded.
In 2017, the average cost per workplace injury was $39,000 – this figure includes wage losses, medical expenses, and administrative expenses (Work Injury Costs, n.d.). This statistic highlights the fact that companies, who must focus on profitability, cannot ignore the importance of a safety program. In fact, “various studies reflect correlations between proactively investing in occupational safety and health and experiencing lower incident rates and higher profit margins.” (Druley, 2019).
Considering that safety has a budget (like all other components of business), companies must be strategic in how they spend their hard-earned dollars. So, what safety program elements will give you the biggest bang for your buck in terms of safety impact? To answer this question, we must consider each component of a safety program’s return on investment (ROI). In 2001, research was conducted to understand the benefit-to-cost ratio of various safety program components. This research measured the resources required to establish and maintain each program element as well as each element’s financial impact on the business (Jervis & Collins, 2001). When ranking highest ROI to lowest ROI, program elements were listed as follows:
- Hazard prevention and control
- Assigned personnel/staff, access to and utilization of certified safety professionals, first aid/CPR personnel on all shifts, use of engineering and administrative controls, safety discipline system, etc.
- Management leadership and employee involvement
- Integration of safety into business planning, written policies and programs, assigned safety responsibilities at all levels, readily available resources for safety efforts, annual safety program auditing, programs for continuous improvement, etc.
- Worksite analysis
- Activity hazard analysis (AHA), workplace safety inspections, written hazard reporting systems, incident investigations, trend analysis, etc.
- Review of documentation
- Annual review of written safety program documentation.
- Safety and health training
- Training on safety responsibilities, job-specific hazards, PPE use/maintenance, and emergency drills.
The highest-ranking program element, hazard prevention and control, is a broad term. What does that mean to an organization? According to the study, this category is mainly defined as having access to designated safety professionals. When analyzing the results, the authors proposed that “without core safety staff, the company will not have the resources needed to conduct hazard analyses, develop written safety rules, monitor regulatory compliance, and track corrective actions.” (Jervis & Collins, 2001). When considering ROI and safety efforts, the study finds that a strong safety team and/or representative is the best financial decision a company can make. This is why we safety consultants are passionate about what we do – we bring value to our customers by providing expertise within the field of occupational safety and health. From procedure development and field inspections to long-term staffing and incident response/case management, we bring the highest level of ROI for your hard-earned dollars.
A commitment to workplace safety is something all companies should pledge for moral reasons – it is the right this to do. Nevertheless, it is misguided to believe that this commitment can be made without regard for a company’s financial future. A sound occupational safety and health program benefits the bottom line by reducing workers’ compensation claims, limiting litigation expenses, avoiding regulatory fines, lowering insurance premiums, qualifying for government contracts, and ultimately winning bids. Other benefits of a program are difficult to quantify and include increased employee retention and improved overall morale. When considering the plethora of benefits related to a comprehensive safety program, companies with tight budgets should evaluate return on investment when budgeting their safety dollars.
Evolution Safety Resources is an occupational safety consultation firm based in Raleigh, N.C. Visit our website to learn more about our services. We are proud of what we do and would love to be of assistance.
References
Druley, K. (2019, January 4). The ROI of safety. Retrieved from https://www.safetyandhealthmagazine.com/articles/17819-the-roi-of-safety.
Jervis, S., & Collins, T. R. (2001). Measuring Safety’s RETURN ON INVESTMENT. (cover story). Professional Safety, 46(9),18. Retrieved from http://search.ebscohost.com.libraryresources.columbiasouthern.edu/login.aspx?direct=true&db=bsu&AN=5154027&site
Work Injury Costs. (n.d.). Retrieved from https://injuryfacts.nsc.org/work/costs/work-injury-costs/
Originally posted on GroundBreak Carolinas